Standard Flanges
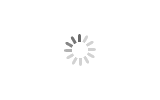
- BOBERRY
- China
- 15-30 Days
- 150-200 Tons/month
Standard flanges:
The national standard flange connection is to fix two pipes, pipe fittings or equipment on a flange, and between the two flanges, with flange pads, bolted together, completed connection. Some fittings and equipment have their own flanges and are also flanged.
Flange connection is an important connection method for pipeline construction. The flange connection is easy to use and can withstand large pressures. Flange connections are widely used in industrial piping. In the home, the pipe diameter is small and low pressure, and the flange connection is not visible. If you are in a boiler room or production site, there are flanged pipes and equipment everywhere.
According to the connection type of flange connection can be divided into: integral pipe flange, steel pipe flange,threaded flange, slip-on welding flange,socket welding flange,lap joint flange,welding neckflange,blind flange,welding neck collar,etc.
Standard Flanges International Standard System
There are two main systems for the international pipe flange standard, namely the European pipe flange system represented by German DIN (including the former Soviet Union) and the American pipe flange system represented by the American ANSI pipe flange. In addition, there are Japanese JIS pipe flanges, but they are generally only used for public works in petrochemical plants, and have little impact internationally. Now introduce the national pipe flanges as follows:
European system pipe flange represented by Germany and the former Soviet Union.
American system pipe flange standard, represented by ANSI B16.5 and ANSI B 16.47.
British and French pipe flange standards, each with two casing flange standards.
In summary, the international standard for pipe flanges can be summarized as two different, non-interchangeable pipe flange systems: a European pipe flange system represented by Germany; the other is represented by the United States. American pipe flange system.
IOS7005-1 is a standard promulgated by the International Organization for Standardization in 1992. This standard is actually a standard for pipe flanges that combines two series of pipe flanges from the United States and Germany. The pipe flange connections of the two systems are different in size and cannot be matched.
The pipe flanges of the two systems are most suitable according to the pressure level, that is, the European system is 0.25, 0.6, 1.0, 1.6, 2.5, 4.0, 6.3, 10.0, 16.0, 25.0, 32.0, 40.0 MPa, and the American system is 1.0, 2.0. , 5.0, 11.0, 15.0, 26.0, 42.0 MPa.
Production Process
The production process is mainly divided into four types: forging, casting, cutting and rolling.
Casting flange and forged flange
The flanges are cast, the shape of the blank is accurate, the processing volume is small, and the cost is low, but there are casting defects (pores, cracks, inclusions); the internal flow of the castings is poor (if it is a cutting part, the streamline type is worse);
Forged flanges generally have lower carbon content than cast flanges and are not easy to rust. Forgings have good streamlined shape, compact structure and better mechanical properties than cast flanges. If the forging process is improper, large or uneven grains will appear, and hardening cracks will occur. Higher than cast flange.
Forgings can withstand higher shear and tensile forces than castings.
The advantage of the casting is that it can produce a more complicated shape and the cost is relatively low;
The advantage of the forging is that the internal structure is uniform, and there are no harmful defects such as pores and inclusions in the casting;
Different from the production process, the difference between the cast flange and the forged flange, such as the centrifugal flange, is one of the cast flanges.
The centrifugal flange belongs to the production flange of precision casting method. This kind of casting is much thinner than ordinary sand casting structure, and the quality is improved a lot. It is not easy to have problems such as loose structure, pores and trachoma.
First of all, we need to understand how the centrifugal flange is produced and processed by centrifugal casting to make a flat welding flange. The product is characterized by the following process steps:
1 The selected raw material steel is smelted in an intermediate frequency electric furnace to make the molten steel temperature reach 1600-1700 ° C;
2 preheating the metal mold to 800-900 ° C to maintain a constant temperature;
3 start the centrifuge, and inject the molten steel in step 1 into the metal mold after preheating in step 2;
4 castings are naturally cooled to 800-900 ° C for 1-10 minutes;
5 Cool with water to near normal temperature, demoulding to remove the casting.
Let's take a look at the production process of forged flanges:
The forging process generally consists of the following steps: selecting high-quality billet blanking, heating, forming, and forging cooling. The forging process is free forging, die forging and film forging. At the time of production, different forging methods are selected according to the quality of the forgings and the number of production batches. The free forging productivity is low, the machining allowance is large, but the tool is simple and the versatility is large, so it is widely used for forging a single piece and a small batch of forgings with a simple shape. Free forging equipment includes air hammer, steam-air hammer and hydraulic press, which are suitable for the production of small, medium and large forgings. Die forging has high productivity, simple operation, and easy mechanization and automation. The die forgings have high dimensional accuracy, small machining allowance, and the fiber structure distribution of the forgings is more reasonable, which can further improve the service life of the parts.
The basic process of free forging: When free forging, the shape of the forging is gradually forged by some basic deformation process. The basic processes of free forging are upsetting, lengthening, punching, bending and cutting.
Upsetting Upsetting is an operation in which the raw material is forged in the axial direction to reduce its height and increase the cross section. This procedure is commonly used for forging gear blanks and other disc-shaped forgings. The ups and downs are divided into two types: all upsetting and partial forging.
Lengthening Lengthening is a forging process that increases the length of the blank and reduces the section. It is usually used to produce shaft blanks, such as lathe spindles and connecting rods.
Punching A forging process in which a punch punches a through hole or a through hole without using a punch.
Bending A forging process that bends a billet into a certain angle or shape.
Torting A forging process that rotates a portion of a blank relative to another portion by a certain angle.
Cutting the forging process of dividing the blank or cutting the material.
Die forging
The die forging is collectively referred to as model forging, and the heated blank is placed in a forging die fixed to the die forging device to be forged. 1. Basic process of die forging The process of die forging: cutting, heating, pre-forging, final forging, punching, trimming, quenching and tempering, shot peening. Commonly used processes are upsetting, lengthening, bending, punching, and forming.
Common die forging equipment Common die forging equipment includes die forging hammer, hot die forging press, flat forging machine and friction press.
Generally speaking, forged flanges are of better quality, generally produced by die forging, with fine crystal structure and high strength, of course, the price is also more expensive.
Both the cast flange and the forged flange are common methods of manufacturing flanges. See the strength requirements of the parts to be used. If the requirements are not high, you can also use the turning flange.
Cutting flange
On the middle plate, the disk with the inner diameter and the inner diameter of the flange with the processing amount is directly cut out, and the bolt hole and the water line are processed. The flange thus produced is called a cut flange, and the maximum diameter of such a flange is limited to the width of the middle plate.
Rolling flange
The process of cutting the strips with the middle plate and then rolling them into a circle is called rolling, and is used for the production of some large flanges. After the coiling is successful, the welding is carried out, and then the flattening is performed, and then the process of the waterline and the bolt hole is processed.
Production standards
National standard: GB/T9112-2000 (GB9113·1-2000~GB9123?4-2000)
Ministry of Chemical Industry Standards: HG5010-52~HG5028-58, HGJ44-91~HGJ65-91, HG20592-2009 Series, HG20615-2009 Series
Ministry of Machinery Standard: JB81-59~JB86-59, JB/T79-94~JB/T86-94, JB/T74-1994 [1] Pressure vessel standard: JB1157-82~JB1160-82, JB4700-2000~JB4707- 2000 B16.47A/B B16.39 B16.
We will always choose the most appropriate process for each forging item, in order to manufacture product of stable quality during the shortest leading time. We guarantee our delivery product has the longest service life of similar products while at low cost to the extremely....more